Navigating the World of OEM LPG Rubber Hose Manufacturing
The world of manufacturing is a complex web of interdependent industries, where each component plays a crucial role in the overall functioning of machinery and equipment. Among these components, OEM (Original Equipment Manufacturer) LPG (Liquefied Petroleum Gas) rubber hoses stand out as essential conduits that ensure the safe and efficient transportation of fuel. The production of these hoses in specialized factories is a testament to the meticulous engineering and quality control required in this sector.
OEM LPG rubber hose factories specialize in creating tailor-made solutions for various applications. These facilities are equipped with state-of-the-art technology and employ skilled professionals who understand the intricacies of designing and fabricating hoses that can withstand the high pressures and corrosive properties of LPG. The process begins with selecting the appropriate materials, typically a combination of synthetic and natural rubber compounds, which offer both flexibility and durability. These materials must adhere to strict industry standards to guarantee their effectiveness and safety in handling volatile substances such as LPG.
The design phase is equally important, as it involves calculating the exact specifications needed for each hose to perform optimally. Engineers use advanced software to model the hose's behavior under different operating conditions, ensuring that the final product can handle the anticipated pressure ranges and temperature fluctuations without failure Engineers use advanced software to model the hose's behavior under different operating conditions, ensuring that the final product can handle the anticipated pressure ranges and temperature fluctuations without failure
oem lpg rubber hose factories. Additionally, the design incorporates features like reinforced layers and sophisticated joinery techniques to prevent leaks and increase the longevity of the hose
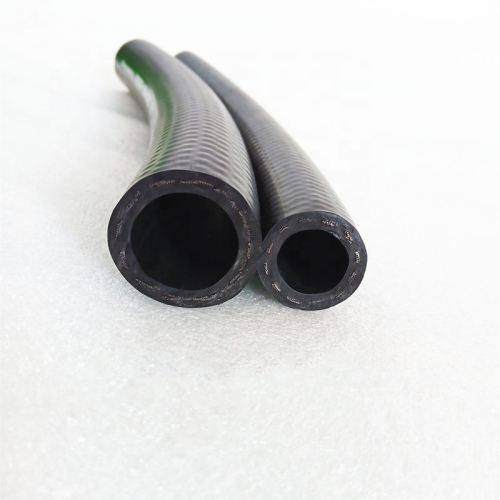
.
Once the design is finalized, the manufacturing process commences. This stage demands precision and attention to detail, as any imperfection can compromise the integrity of the hose. From mixing raw materials to extrusion, curing, and assembly, each step is performed with exacting standards. Quality control inspectors monitor every aspect of production, from material selection to the finished product, to ensure that each hose meets or exceeds performance criteria.
In conclusion, OEM LPG rubber hose factories serve as vital hubs of innovation and reliability within the industrial landscape. They embody a commitment to excellence by producing custom-fitted solutions that safeguard against hazards associated with LPG transportation. As technology advances and demands for efficiency increase, these factories continue to push the boundaries of what is possible in rubber hose engineering, ensuring that their products remain at the forefront of performance and safety.