A fuel hose factory serves as an essential cornerstone in the production and supply chain for a wide array of industries, from automotive to aerospace. The complexities involved in manufacturing fuel hoses require not just high technical expertise but also a commitment to quality and safety. Delving into the intricacies of such operations offers an insightful glimpse into a processes rich with innovation, precision, and reliability.
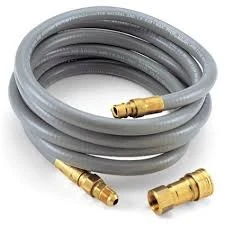
Fuel hoses need to withstand an array of harsh conditions, including extreme temperatures, pressures, and exposure to various fuels and chemicals. This implies that the materials used in their production are subject to strict quality controls and demanding durability standards. The choice of material often varies dependent on the intended application, ranging from nitrile rubber, which offers good resistance to petroleum products, to viton, which is known for superior heat and chemical resistance.
The manufacturing process generally begins with material selection and compounding. This is where the initial layers of rubber are formed, blended with various additives to enhance their strength, elasticity, and resistance to potential environmental stressors. Expert chemists and engineers are pivotal here, given their ability to formulate and innovate compounds that meet unique client specifications. During this phase, a series of stringent tests are conducted to ensure each batch meets pre-established industry standards.
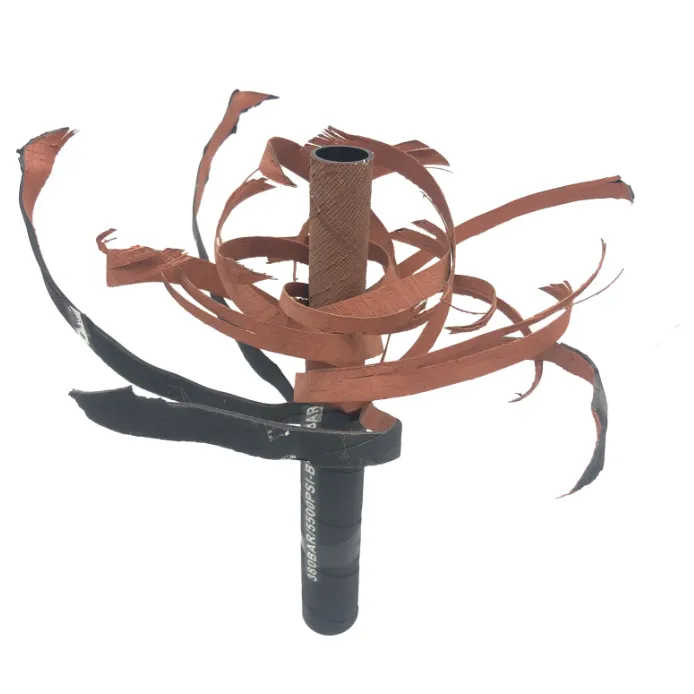
Extrusion follows, where the rubber compound is formed into a tube shape. Precision control is necessary to maintain consistent thickness and diameter, both vital factors that influence the hose’s performance and safety. Advanced extrusion machinery, primarily CNC (Computer Numerical Control) systems, provide the high level of control needed to produce hoses that comply with exacting industrial standards. These machines are operated by experienced technicians trained to spot and rectify any anomalies during production, ensuring product quality at every stage.
The vulcanization process is next, whereby the extruded hoses are heated and pressurized to solidify and set the rubber. This step is where the hose gains its elastic properties, making it resilient to the demands of fluid transfer. The technical precision required in managing temperature and pressure during vulcanization is crucial; hence, only specialized personnel with comprehensive knowledge of the process undertake this task to guarantee optimal physical properties.
fuel hose factory
Post-vulcanization involves braiding or knitting fibrous materials around the rubber to enhance strength. This structural reinforcement, often involving materials like Kevlar or stainless steel, is critical to the hose's ability to endure mechanical stress without failure. The alignment of fibers must be precise, and any deviation can affect the integrity of the finished product, making this phase equally reliant on expert supervision.
Quality assurance is non-negotiable in a fuel hose factory. A series of rigorous tests, such as hydrostatic and burst pressure testing, is crucial in ensuring each hose can withstand the pressures expected in real-world applications. Laboratories equipped with state-of-the-art testing facilities, like tensile testers and chemical analyzers, play a vital role at this stage. Their outputs not only affirm the durability but also certify compliance with regulatory standards such as SAE, ISO, and API.
Moreover, achieving and maintaining certifications such as ISO 9001 is a testament to a factory's dedication to excellence and continuous improvement. It reflects a systematic, process-driven approach to manufacturing, underpinning the plant’s commitment to producing safe, reliable hoses.
Beyond manufacturing, robust customer support and after-sales service enhance a factory’s reputation within the industry. Trust is cultivated by providing detailed installation guides, usage recommendations, and maintenance tips to end users. When engineers and service personnel engage transparently with clients to address concerns, they help build long-term relationships anchored in confidence and reliability.
Fuel hoses, while seemingly straightforward components, are integral to the safe and efficient operation of countless machines and vehicles. The factories that produce them are driven by a dedication to expertise and an unwavering commitment to quality. From raw material to finished product, the journey of a fuel hose reflects a meticulous orchestration of science, precision, and skill—an embodiment of experience, expertise, authoritativeness, and trustworthiness.