High pressure hoses are indispensable components in various industries, known for their resilience and ability to safely transfer fluids under pressure. The significance of selecting the right high pressure hose cannot be overstated, as it ensures the uninterrupted performance and safety of industrial operations. Drawing from years of expertise, this guide provides insights into the vital aspects of high pressure hoses, bolstering experience, professionalism, authority, and trust—a primer for those seeking to optimize their industrial applications.
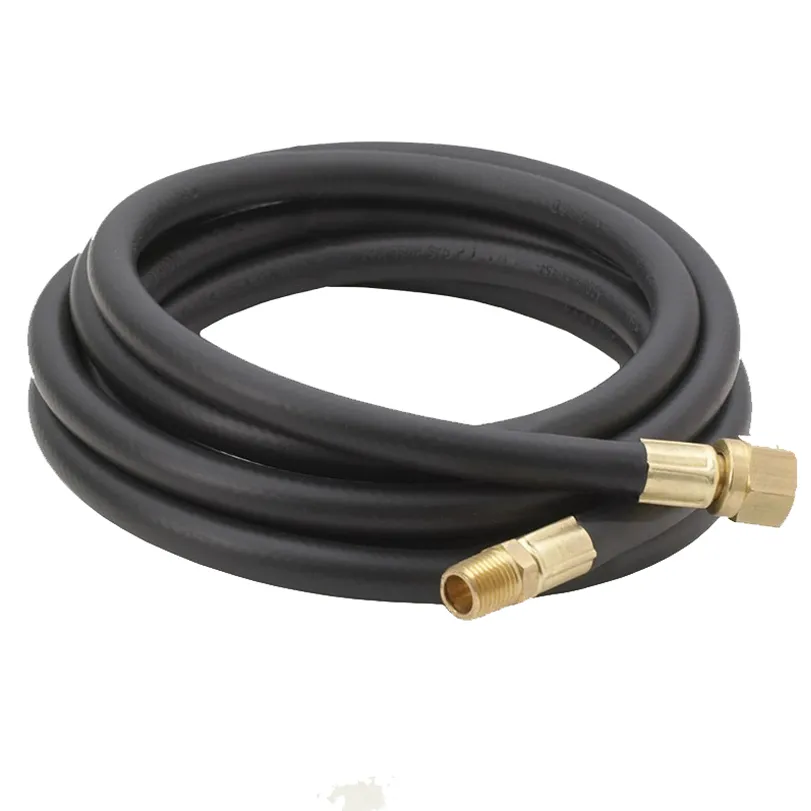
High pressure hoses are engineered to withstand immense pressure while maintaining flexibility and light weight. This balancing act is critical for tasks ranging from hydraulic systems in heavy machinery to high-intensity water-blasting equipment. The construction typically involves multiple layers of materials such as rubber, thermoplastic, or PTFE, which are reinforced by braided or spiral steel wire. An intimate understanding of these material properties is foundational when evaluating a hose's performance metrics like pressure range, temperature tolerance, and fluid compatibility.
The hallmark of a quality high pressure hose is its pressure rating, commonly specified in PSI (pounds per square inch). However,
the pressure rating does not singularly determine the hose's capability. It's the nuanced understanding of burst pressure, working pressure, and safety factor that elevates an expert's choice. The burst pressure denotes the maximum pressure a hose can endure, whereas the working pressure is what it can handle during regular operation. Professionals rely on a safety factor—a buffer between the working and burst pressure—to fend off unexpected surges, thereby safeguarding equipment and operators.
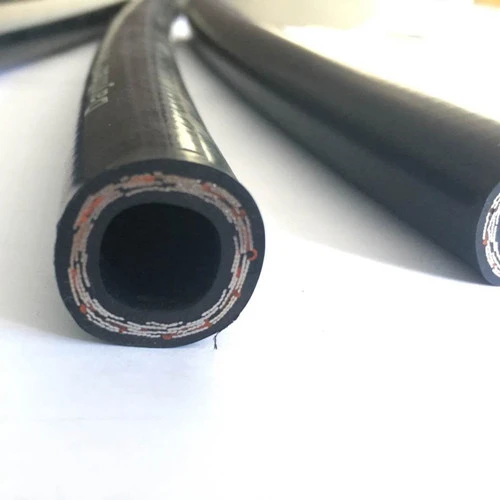
When selecting a high pressure hose, expertise guides a user to consider the hose's application environment. Factors such as exposure to chemicals, extreme temperatures, and potential abrasion inform the right material choice. For instance, PTFE-lined hoses exhibit robust chemical resistance, making them ideal for corrosive environments, while hoses with an outer layer of abrasion-resistant material excel in rugged settings.
high pressure hose
Authoritativeness in this domain is exhibited by adhering to industry standards, such as those from the International Organization for Standardization (ISO) and the Society of Automotive Engineers (SAE). These standards act as benchmarks for safety, durability, and performance, ensuring reliability and public trust. Experience complements authority—seasoned users possess a repository of troubleshooting insights drawn from on-the-ground scenarios, like detecting wear symptoms and executing preventive measures that extend hose longevity.
Trustworthiness involves transparency in maintenance practices. Regular inspection routines identify potential issues early, such as kinks, leaks, or signs of wear in fittings and connections. Correctly documenting inspections and maintenance checks aligns with best practices, reinforcing the dependability of the system. In addition, sourcing from reputable manufacturers who provide warranties and comprehensive technical support enhances confidence between buyers and suppliers.
In conclusion, the true mastery over high pressure hoses is achieved by harmonizing practical experience, profound expertise, adherence to authoritative standards, and a robust foundation of trust. This synthesis not only ensures operational efficiency but fortifies the integrity of industrial processes where these hoses play a pivotal role. Whether deploying them in agriculture, construction, or automotive industries, the overarching goal remains to navigate pressures with precision and safeguard productivity with unwavering confidence.