Exploring the world of hydraulic hoses opens myriad pathways into industrial efficiency and precision. These essential components connect various devices in hydraulic systems, transferring fluid to enable machinery to operate with power and control. The versatile nature of hydraulic hoses makes them indispensable in sectors ranging from construction to agriculture, automotive to aerospace.

Understanding the intricacies of hydraulic hose design can greatly enhance one's experience in selecting the right product for the job.
Hydraulic hoses are typically constructed from three layers the inner tube, a reinforcement layer, and an outer protective layer. The inner tube is crafted from a flexible material compatible with the hydraulic fluid to ensure smooth flow and prevent erosion. The reinforcement layer, often made from fiber or a braided wire, provides the necessary strength to withstand high pressures. Lastly, the outer layer shields from environmental factors like ultraviolet light, abrasion, and chemicals.
The expertise in designing and manufacturing hydraulic hoses lies in balancing these layers to meet specific pressure ratings and application demands. An expert understands that the hydraulic hose's diameter must be precisely calculated to minimize pressure drops and optimize fluid flow. Adequate fitting selections also play a crucial role; they must match the hose in size, material, and pressure rating to prevent leaks and enhance the system's reliability.
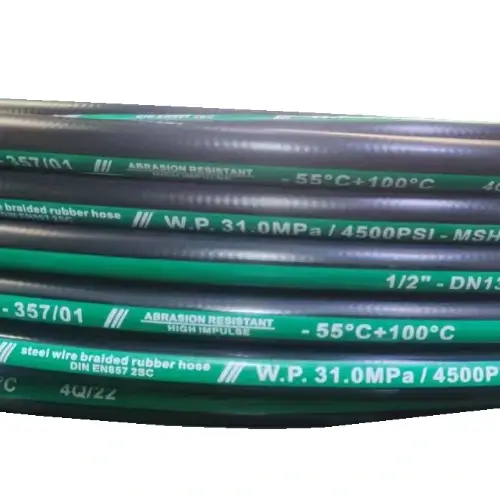
hydraulic hose
With authority in hydraulic hose utilization, it becomes evident that regular maintenance and timely replacement are paramount. Even the most robust hoses can wear out due to high-pressure cycles and external conditions. An adept professional regularly inspects hoses for signs of wear, such as blistering, cracking, and exposed reinforcement wires, which could indicate potential failure. Moreover, replacing hoses before they reach their maximum service life can prevent catastrophic failures, costly downtime, and ensure safety in operations.
Trustworthiness in hydraulic hose producers and suppliers is non-negotiable. Quality and adherence to stringent manufacturing standards, such as ISO 18752 or SAE J517, must be verified to guarantee product performance. Trusted manufacturers not only follow these guidelines but also subject their products to rigorous testing procedures, including impulse testing, leak testing, and pressure testing. Establishing trust with customers further involves providing data sheets and support for installation, ensuring users have all necessary information for effective usage.
Enhanced by experience, expertise, authority, and trustworthiness, an optimal hydraulic hose selection can lead to improved system performance, reduced downtime, and maximized productivity. Whether one is retrofitting an existing system or designing a new one, partnering with a reputable supplier and consulting with hydraulic specialists provides invaluable insights that align with application-specific needs. Consequently, the efficient functioning of hydraulic systems, fueled by well-chosen hoses, remains a cornerstone of successful industrial operations, driving forward projects with precision and reliability.