In the realm of industrial applications and automotive mechanics, the oil hose stands as a critical component, often operating behind the scenes yet ensuring the smooth functioning of complex machinery. As an essential conduit for transferring oil, understanding its role, selection criteria, and maintenance can not only enhance equipment efficiency but also reinforce safety protocols.
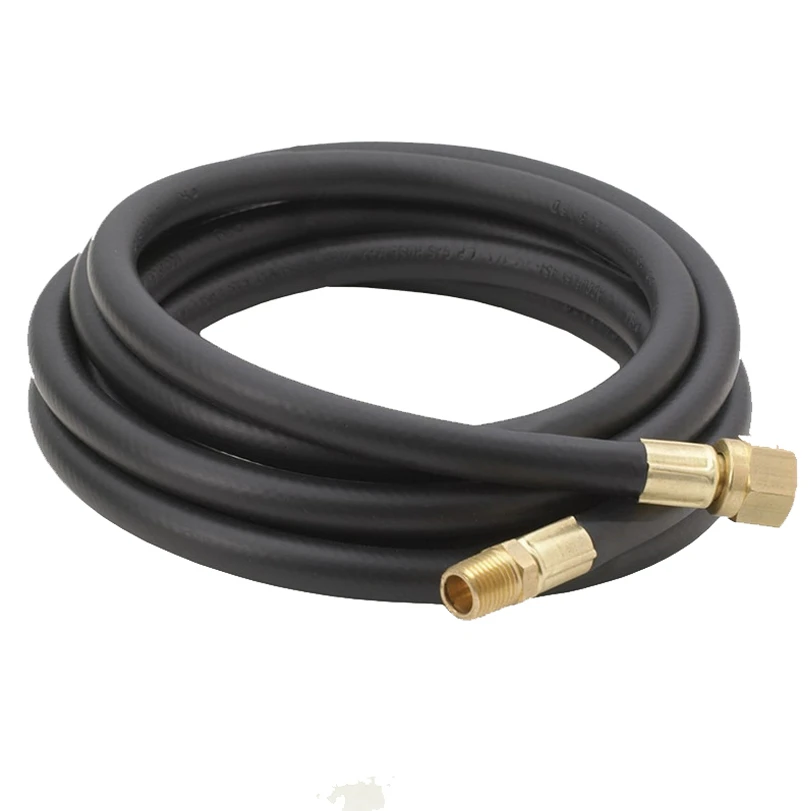
Oil hoses are designed to handle the arduous demands of transferring oil under varying pressures and temperatures. These hoses are indispensable in sectors such as automotive, marine, manufacturing, and construction, where they facilitate the movement of lubricants that are crucial for machinery operation. A high-quality oil hose is resilient, capable of withstanding external and internal stresses, and impervious to the chemical composition of the oil it conveys.
When selecting an oil hose, the primary considerations involve the specific needs of the application. The material is paramount—typical choices include synthetic rubber, thermoplastics, and composites, each offering unique advantages. Synthetic rubber hoses, for instance, are known for their flexibility and durability, often employed in automotive settings. Thermoplastics provide enhanced resistance to chemicals and abrasions, making them suited for industrial scenarios. Composites, combining various materials, offer excellent stress tolerance and versatility across different environments.
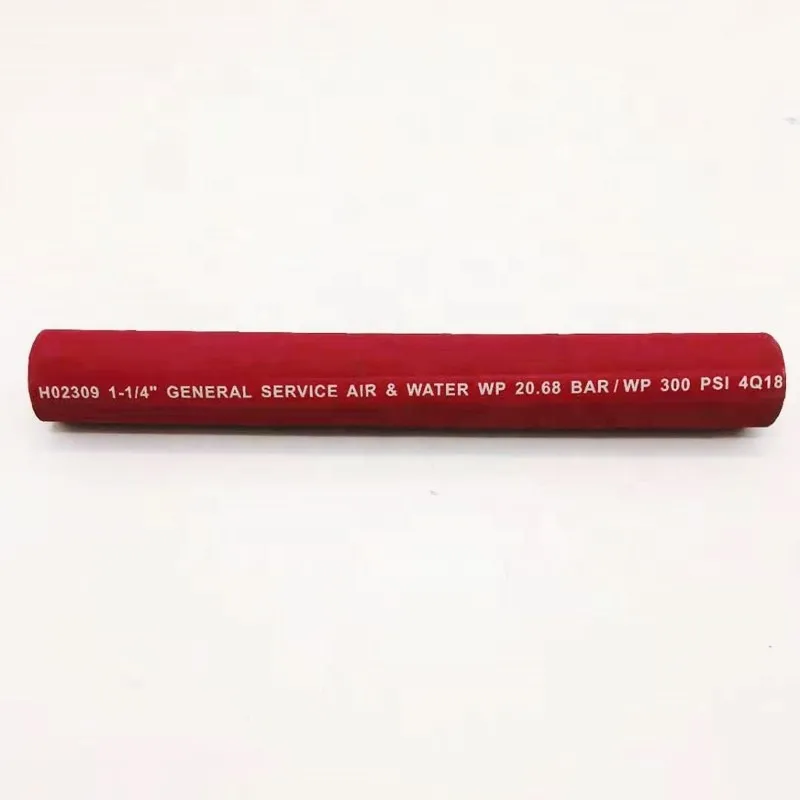
Beyond material choice, the size specifications of an oil hose are critical. These specifications ensure the optimal flow capacity and pressure rating for the intended application, reducing the risk of malfunctions or safety hazards. Incorrect sizing can lead to a decrease in flow efficiency or, worse, hose rupture, leading to downtime and potential safety concerns.
Incorporating expertise into hose maintenance extends the lifespan and functionality of the oil hose. Regular inspections are vital, focusing on any signs of wear and tear, such as cracks, blisters, or abrasions.
These indicators usually precede failures that could compromise the entire system. Furthermore, understanding the hose's operating limits regarding pressure and temperature can prevent overburdening the hose, which is a common cause of premature hose failure.
oil hose
Safety is intrinsically tied to the reliability of oil hoses. A well-maintained hose assures not just the optimal performance of machinery but also guards against leaks and spills that could lead to environmental and safety hazards. In high-risk environments, this reliability is paramount, where any failure could translate into significant economic loss or safety incidents.
The trustworthiness of an oil hose, therefore, is as much about its manufacturing standards as it is about the expertise applied in its maintenance and installation. Selecting hoses from reputable manufacturers who adhere to certified quality standards, such as ISO 9001, adds an additional layer of assurance regarding their performance. Furthermore, engaging experienced technicians for installation ensures that the hose is fitted and routed correctly, thus optimizing its operational lifespan.
In the ever-evolving market of oil hoses, staying informed about advancements and innovations can be beneficial. The development of nanomaterials and smart technologies, for instance, holds promise for enhancing the performance and intelligence of oil hoses, incorporating advanced monitoring systems that predict potential failures even before they occur.
In conclusion, oil hoses may be a single component within complex systems, but their importance cannot be overstated. Emphasizing expertise in selection, maintenance, and adherence to safety standards, alongside leveraging innovations, ensures that they remain robust, efficient, and reliable. Building on a foundation of trust and authority in choosing and handling oil hoses directly translates to improved performance and safer industrial environments.