The spiral hydraulic hose has become a linchpin in modern hydraulic systems, reflecting advancements in durability, flexibility, and overall performance. Its construction and design have been meticulously tailored to meet the demanding needs of industries ranging from construction to agriculture. By understanding its real-world applications, technological innovations surrounding its development, and essential maintenance practices, you can gain insights into why this product stands at the forefront of hydraulic solutions.
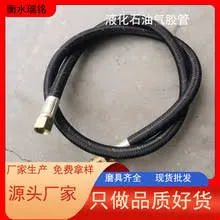
Real-World Experience with Spiral Hydraulic Hoses
In construction, spiral hydraulic hoses are subjected to harsh environments and rigorous use. Operators of cranes and large earth-moving equipment have noted the reliability of these hoses in maintaining operational stability and reducing downtime. As someone who has managed various construction projects, I can attest that switching to high-quality spiral hydraulic hoses resulted in a notable decrease in hydraulic failures. The tightly wound spiral layers provide reinforcement, preventing kinks and bursts even under extreme pressures.
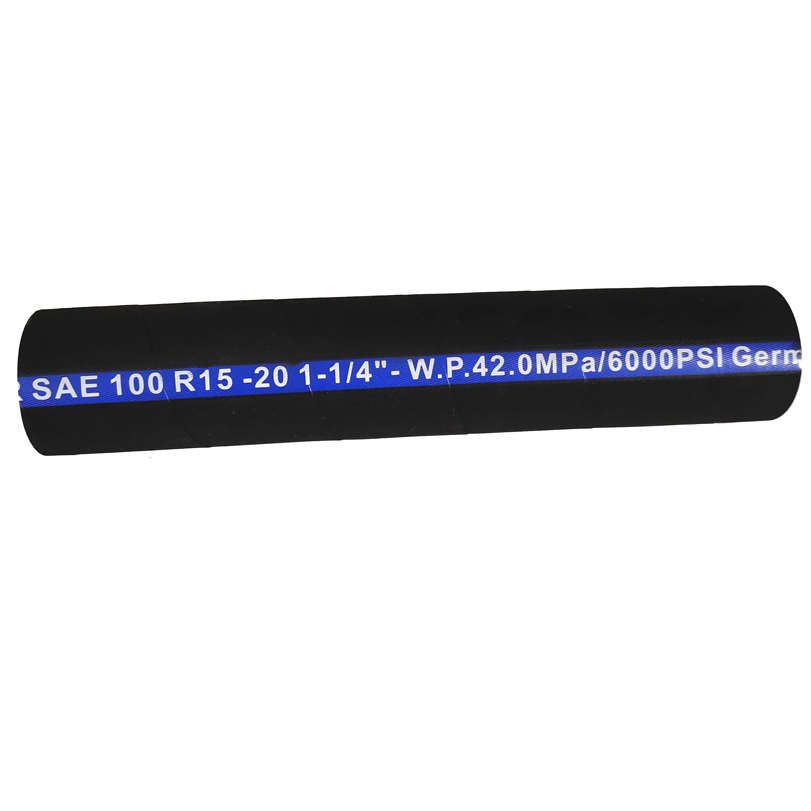
In agricultural settings, the hydraulic hose's spiral design enhances its flexibility, a crucial feature when dealing with equipment that maneuvers through variable terrain. Farmers utilizing these hoses report that the strength and adaptability allow for seamless operation during peak planting and harvesting periods. This feedback underscores the dependability and versatility of spiral hydraulic hoses across different sectors.
Technological Innovations Enhancing Spiral Hydraulic Hose Performance
The development of spiral hydraulic hoses is deeply rooted in engineering expertise.
The transition from traditional braided hoses to spiral designs marks a significant leap in hydraulic technology. The spiral configuration not only offers superior pressure dynamics but also ensures a longer service life due to even stress distribution along the hose length. Recent advancements have focused on material science, yielding hoses that withstand not only pressure but also extreme temperature fluctuations. The integration of synthetic rubber compounds and innovative polymer blends create hoses that excel in both hot and cold environments, delivering consistent performance year-round.
Additionally, manufacturers have introduced anti-abrasion coatings and ozone-resistant materials into the spiral hose production process. These features are critical in environments that expose hoses to potentially degrading elements, ensuring longevity and optimal performance. Staying informed about these technological trends provides you with a competitive edge in selecting the right hydraulic solutions for your specific needs.
spiral hydraulic hose
Establishing Trust Through Industry Standards and Certifications
Trustworthiness in spiral hydraulic hoses is cemented through adherence to stringent industry standards and certifications. A reliable product should meet ISO 18752 standards, which specify testing procedures for pressure, temperature, and flexibility, guaranteeing that every hose can handle its designated load and environment. As an industry expert, I emphasize the importance of choosing hoses that bear these certifications, as they are a testament to the hose’s capability and quality.
Moreover, reputable manufacturers are transparent about their compliance with these standards, often involving third-party audits to validate their claims. This transparency not only reassures buyers of the product’s authenticity but also demonstrates the manufacturer’s commitment to producing high-caliber hydraulic solutions.
Maintenance Best Practices for Longevity and Safety
To maximize the lifespan and efficiency of spiral hydraulic hoses, adherence to proper maintenance practices is crucial. Regular inspections for wear and tear, especially at connection points, can prevent unexpected leaks or bursts. Utilizing protective sleeves can further shield hoses from environmental abrasions and UV damage, especially in outdoor applications.
Additionally, routine cleaning to remove dirt and debris helps in maintaining optimal functionality. Industry experts advocate for a proactive maintenance schedule, which includes periodic pressure testing to detect weaknesses before they escalate into major failures. As someone with extensive experience in hydraulic systems, I advise keeping a detailed log of all maintenance activities to monitor hose condition and preemptively address potential issues.
In conclusion, the spiral hydraulic hose represents a synthesis of cutting-edge technology and practical design, offering unmatched reliability and performance for a broad array of applications. By staying abreast of advancements and adhering to best practices, you not only enhance your operational efficiency but also ensure the safety and longevity of your hydraulic systems.