Hydraulic hose pipe fittings play a pivotal role in diverse industries where fluid power is a necessity, ranging from construction to manufacturing, agricultural to automotive industries. Understanding the intricacies of these components not only enhances system performance but is integral for ensuring operational safety and efficiency. As someone with years of experience in hydraulic systems, I can assert that selecting the correct hose fittings requires more than just a basic understanding; it demands expertise in system requirements, material compatibility, and maintenance practices.
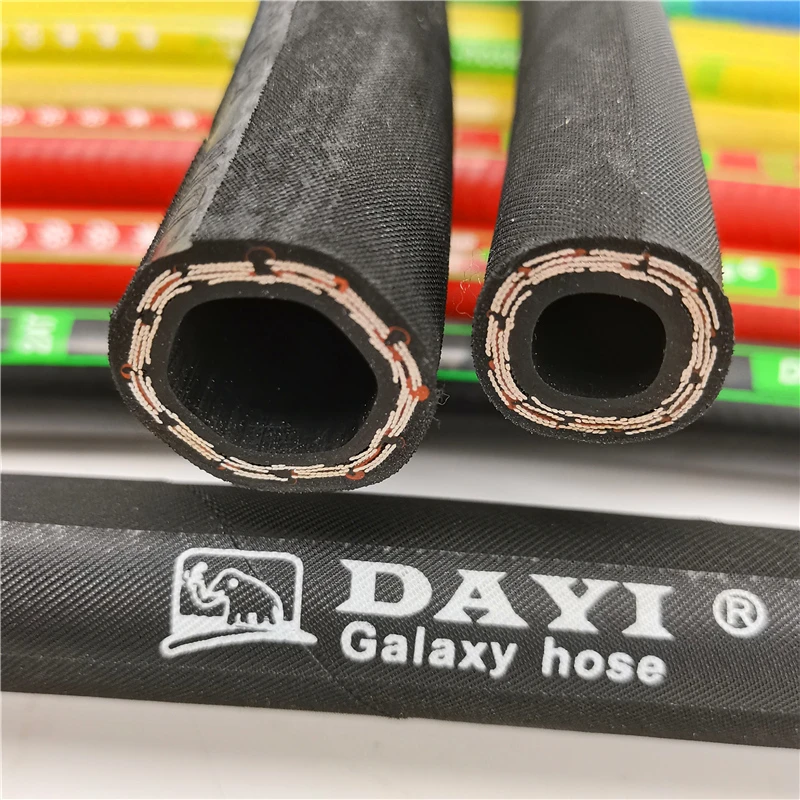
A hydraulic hose fitting acts as a connector between hoses and other system elements, enabling the seamless passage of hydraulic fluids. A critical factor for optimal performance involves selecting fittings that meet the precise specifications of your application. An ill-suited fitting could lead to operational failures, costly downtime, and even safety hazards. As such,
understanding the types and specifications of hydraulic hose fittings is paramount.
Expertise in this field would emphasize the importance of material selection. The material of the fitting is essentially tied to the fluid type, system pressure, and environmental conditions. The most common materials used in fittings include steel, brass, and stainless steel. Steel fittings offer durability and are apt for high-pressure applications, but they can be susceptible to rust if exposed to certain environments. In contrast, brass fittings are more corrosion resistant, making them suitable for marine applications but can falter under high-pressure scenarios. Stainless steel fittings offer both corrosion resistance and robust performance under various pressures and temperatures, often considered the premium choice for harsh conditions.
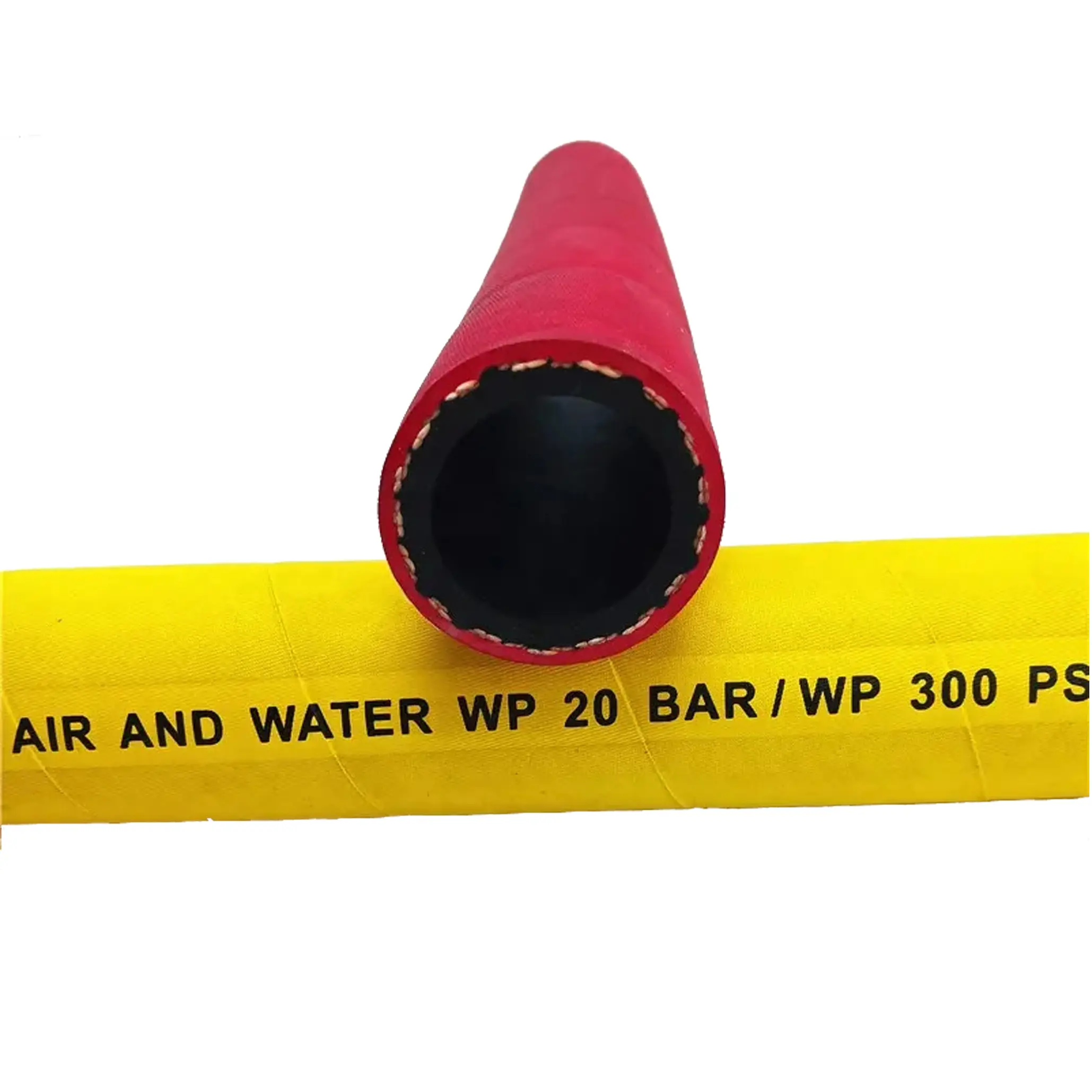
Another point of consideration is the design type of the fitting, such as crimp, push-to-connect, or bite-to-wire fittings. Crimp fittings, offering reliable and permanent connections, pair well with high-pressure systems. Push-to-connect fittings provide ease of use and are often found in low-pressure systems, allowing for quick assembly and disassembly without the need for tools. Bite-to-wire fittings excel in firmly securing the hose to the fitting, which is vital for systems subject to vibration or high pulsation.
hydraulic hose pipe fittings
An authoritative knowledge extends to thread types, ensuring compatibility across system components. Thread types like BSP, NPT, and JIC may vary based on regional standards, with each offering distinct sealing methods. Mismatched threads can lead to leakage, system inefficiency, and potential failures. Therefore, reliance on matching standards not only enhances system reliability but consolidates trust in system integrity.
Trustworthiness in hydraulic hose pipe fittings does not merely rely on selection but extends to maintenance protocols. Regular inspection for wear and tear, signs of corrosion, or loosening can prevent catastrophic system failures. A preventive maintenance schedule should be implemented, ensuring that the longevity of the fittings aligns with system operational goals. Utilizing fittings from reputable manufacturers known for rigorous testing and quality assurance further cements system reliability and user trust.
It is also advisable to work with certified professionals or suppliers when in doubt. These experts provide invaluable insights into cutting-edge technology and developments, ensuring that you are leveraging the best available solutions to optimize your system’s performance.
In conclusion, hydraulic hose pipe fittings are more than mere connections in a system; they are critical components that demand precise understanding and informed decision-making. As industries evolve and demands intensify, staying informed and educated about the latest trends, materials, technologies, and standards becomes essential. By prioritizing experience, expertise, authority, and trustworthiness in selecting and maintaining these fittings, one ensures not only the optimal performance of their hydraulic systems but also safeguards the integrity and safety of their operations.